Ultraviolet (UV) radiation is a powerful degrading factor, particularly for plastic materials. Despite this, some manufacturers continue to use plastic for casings and components of sterilizers exposed to direct UV radiation. This significantly reduces the lifespan of the equipment and increases the risk of failure. The solution to this issue lies in replacing vulnerable materials with more durable alternatives.
How UV radiation affects plastic
Plastic components deteriorate under UV exposure for several reasons:
- Heating – Prolonged direct exposure to UV radiation causes a substantial increase in plastic temperature, leading to deformation and a decline in mechanical strength.
- Photochemical degradation – UV light induces destructive molecular changes, resulting in discoloration, cracking, brittleness, and eventual material failure.
To minimize the effects of UV radiation, plastic components should either be shielded by protective screens or entirely replaced in areas exposed to UV light. This approach extends the operational lifespan of the equipment and enhances its overall performance.
Common mistakes in using plastic in UV sterilization units
A critical mistake made by some manufacturers is incorporating plastic in UV water sterilization systems. Continuous UV exposure causes irreversible damage to plastic parts, including deformation, cracking, and loss of structural integrity. As a result, not only does the equipment’s service life decrease, but its safety is also compromised—especially for devices operating with water.
The image illustrates the consequences of using plastic components in UV water sterilization systems. To prevent such damage, fluoroplastics should be used instead, as shown on the left.
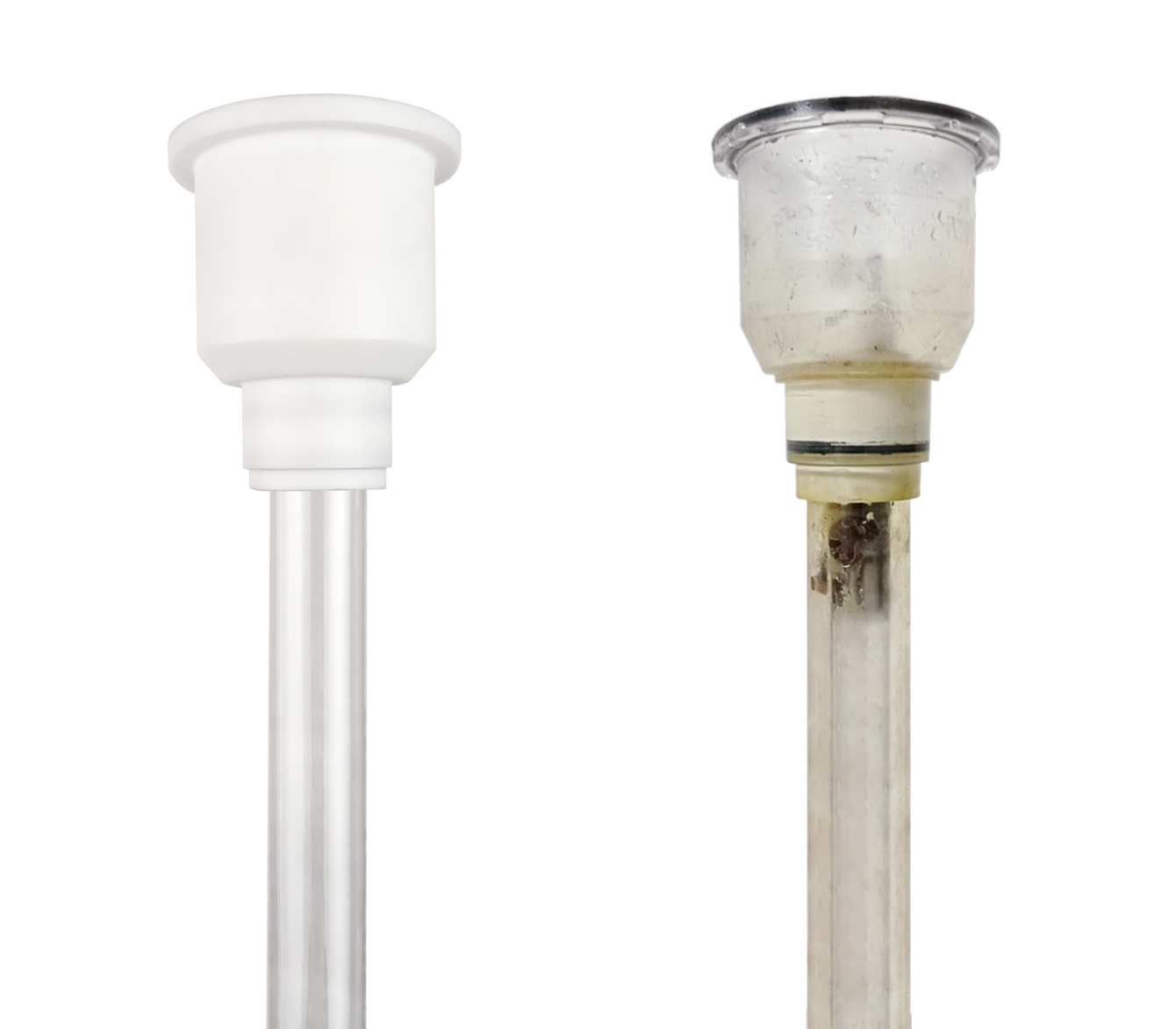
Fluoroplastics: an innovative solution
UVL offers a reliable solution to this challenge—the use of fluoroplastics, a material with exceptional resistance to UV radiation. Key advantages include:
- Lightweight – Fluoroplastics are significantly lighter than metal, facilitating easier transportation and installation.
- UV resistance – The material retains its properties even under prolonged exposure to high-energy UV radiation.
- Durability – Fluoroplastics withstand significant mechanical stress and remain resistant to environmental factors.
One example of fluoroplastic application is the sealing unit housing in UVL-MOD submersible UV modules, designed for water disinfection. These components maintain their functionality even under harsh operating conditions, ensuring the reliability and longevity of the entire system.
Replacing plastic with fluoroplastics in UV-exposed environments not only extends equipment lifespan but also enhances operational safety. At UVL, we prioritize cutting-edge materials to deliver solutions that combine quality, durability, and reliability.